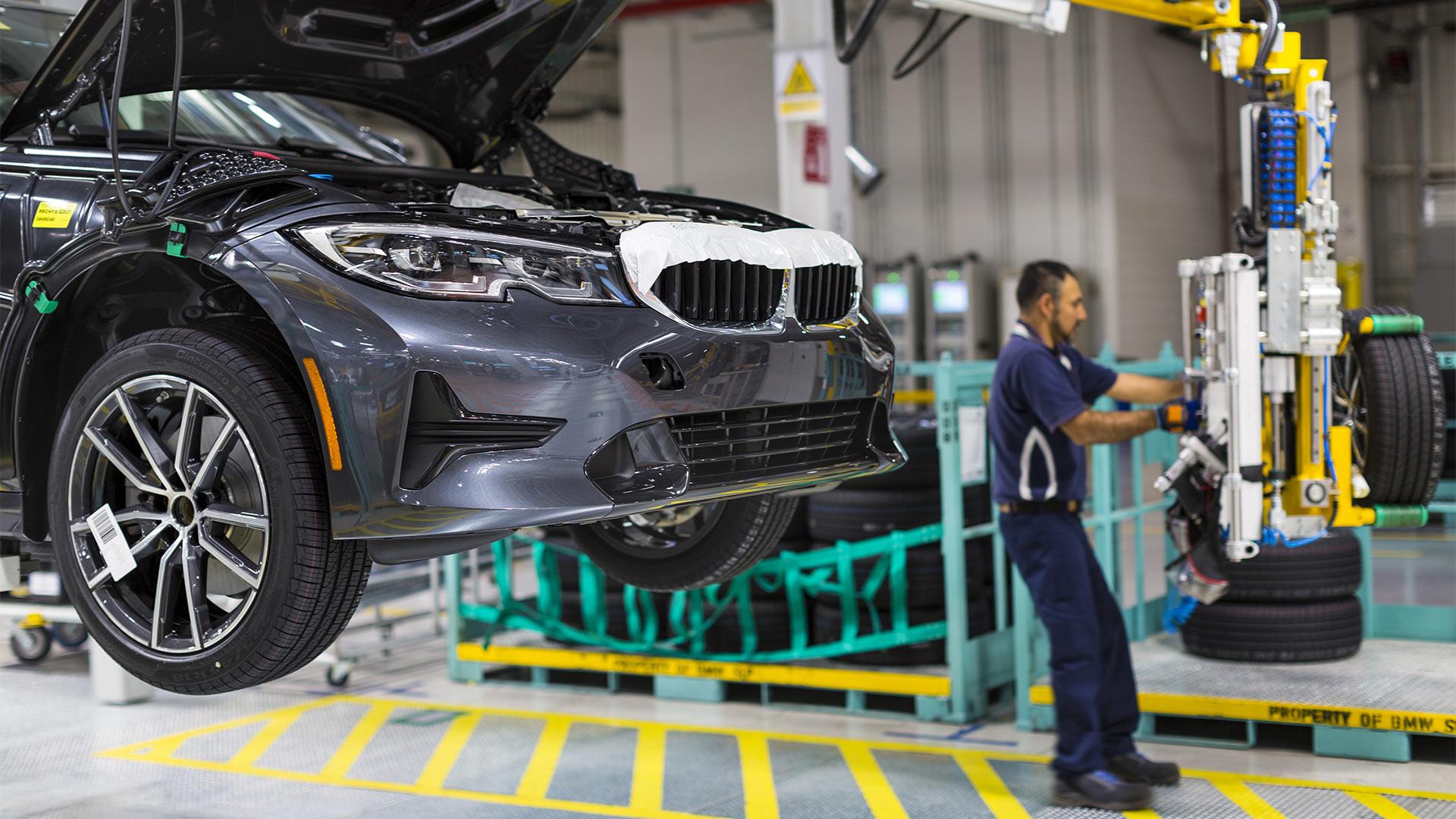
CO2-Ausstoß bei Produktion Der weite Weg zum klimaneutralen Auto
Klimaneutral mit dem Auto fahren, das geht beispielsweise mit Strom aus Erneuerbaren Energien. Doch was dabei vergessen wird: Bereits bei der Produktion eines Autos fällt tonnenweise CO2 an. Wie lässt sich das ändern?
Ortstermin im niederbayerischen Landshut: Hier betreibt BMW ein Werk für Leichtmetallguss. Der Münchner Autobauer produziert alle wichtigen Aluminiumteile seiner Fahrzeuge selbst. Zum Beispiel den Zylinderkopf für seine Baureihen mit Sechszylindermotoren. Knapp 40 Kilogramm flüssiges Aluminium sind für so einen Kopf notwendig. Ein Roboterarm schwenkt einen überdimensionalen Löffel über die Form aus gepresstem Sand. Dann kippt der Löffel, und das auf 780 Grad erhitzte Leichtmetall fließt in die Form. Vier Minuten später ist der Zylinderkopf fertig, der Roboterarm nimmt das ausgekühlte Bauteil wieder auf.
Ein Mitarbeiter überwacht drei Gießplätze. Werktags sind sie, wie das ganze Werk, in drei Schichten rund um die Uhr in Betrieb. Allein dieser eine Arbeitsplatz lässt erahnen, wie energieintensiv die Produktion eines Autos ist. Um das Aluminium zu schmelzen und für alle möglichen Gussteile im Auto weiterverarbeiten zu können, muss es auf bis zu 900 Grad erhitzt werden. Das geht bislang nur mit Erdgas. Allein dabei fallen gewaltige Mengen Kohlendioxid an.
Recycling hilft beim CO2-Einsparen
Doch auch die Herstellung des Leichtmetalls selbst ist sehr CO2-intensiv. Um die großen Emissionen zu verringern, setzt BMW auf Recycling. Zwei Drittel des Metalls sind wiederverwertetes Material. Das restliche Drittel kommt aus Dubai. Der Zulieferer dort produziert es ausschließlich mit Solarstrom.
Das spart schon mal gegenüber der konventionellen Herstellung erhebliche Mengen des für die Erderwärmung verantwortlichen Kohlendioxids. Doch verpufft dieser positive Effekt nicht wieder, wenn anschließend das mit "grüner" Energie hergestellte Metall über Tausende Kilometer nach Landshut transportiert werden muss?
Martin Bednarz sieht darin kein Problem. Der Experte für grüne Produktionsverfahren an der Technischen Hochschule Ingolstadt verweist auf die "besonders energieintensive Aluminiumherstellung". Deshalb mache es "wirklich viel Sinn, das Material vor Ort mit grünem Strom zu produzieren. Der Transport schlägt dann natürlich noch einmal zu Buche, aber das ist anteilig sehr viel geringer zu gewichten als die Herstellungsenergie", so Bednarz.
Emissionen in der Lieferkette
Ab nächstem Jahr will BMW große Teile seines Aluminiums mit noch weniger CO2-Ausstoß herstellen lassen. In Kanada, mit Wasserkraft und einem neuen Verfahren, das der Zulieferer Rio Tinto entwickelt hat. BMW zufolge spart man damit im Vergleich zur üblichen Produktion 70 Prozent CO2 ein. Für die Chefetage des Autobauers ein wichtiger Schritt Richtung Klimaschutz.
Man müsse auch die Produktion und das Recycling eines Autos im Blick haben, sagt Vorstandsmitglied Joachim Post, der den Einkauf und das Lieferantennetzwerk leitet. "Es ist einfach zu kurz gesprungen, nur die Nutzungsphase eines Fahrzeugs und eines Antriebs alleine zu betrachten. Ganz wichtig sind für uns die CO2-Emissionen in der Lieferkette." BMW habe sich ein ehrgeiziges Ziel vorgenommen: Man wolle "in der Lieferkette plus Nutzungsphase, also in der gesamten Lebenszeit eines Fahrzeugs, die CO2-Emissionen bis 2030 um 40 Prozent gegenüber dem Jahr 2019 reduzieren".
Der Münchner Autobauer ist eigenen Angaben zufolge dabei im Zeitplan. 40 Prozent weniger heißt aber auch: Es entsteht immer noch tonnenweise CO2 bei jedem Auto. Neue Konstruktionsverfahren könnten dieses Problem zumindest ein Stück weit kleiner machen.
Autoteile aus dem 3-D-Drucker
Wie das funktionieren könnte, erforscht Thomas Binder an der Technischen Hochschule Ingolstadt. Der Fachmann für Konstruktion experimentiert dabei mit 3-D-Druckern. In denen hat er beispielsweise schon Felgen hergestellt. Das Besondere daran: Der 3-D-Drucker ermöglicht es, viele große und kleine Hohlräume in die Felge einzubauen. Die Radträger weisen dreidimensionale Waben- und Gitterstrukturen auf.
Das spart Material und Energie und vermindert so letztlich den Ausstoß von Klimagasen, sagt Binder: in der Produktion, aber auch in der Nutzungsphase, da die zu bewegende Masse kleiner werde. Und auch beim Recycling sinke später der Energieaufwand.
"Bei einer Rennsportfelge, die etwa 13 Kilogramm wiegt, haben wir durch diese Technologie zwei bis drei Kilogramm einsparen können." Wenn man dies auf alle Bauteile des Fahrzeuges übertrage, "dann ist dort eine Ersparnis von zehn bis 20 Prozent drin", rechnet Binder vor. Seine Kalkulation versieht er aber mit einem Vorbehalt: "Vorausgesetzt, wir bekommen das Problem mit der Festigkeit unserer gedruckten Aluteile hin."
Denn noch sind die Werkstücke aus dem Drucker bei extremen Belastungen nicht so stabil und bruchsicher wie solche, die im Gussverfahren hergestellt werden. Binder ist aber zuversichtlich, dafür eine Lösung zu finden. "Wir müssen nur die richtige Legierung hinbekommen." Also die Mixtur des Aluminiums so verändern, dass es auch in gedruckter Form die beim Autofahren auftretenden extremen Kräfte ohne Schaden am Metall aushält.
Hoffen auf eine Kreislaufwirtschaft
Im Forschungs- und Innovationszentrum von BMW im Norden Münchens steht im Foyer ein schwarzer E-Mini - ein Cabriolet, von dem nur 999 Stück gebaut werden sollen, eine Sonderedition. Auch für die BMW-Belegschaft ist der kleine Wagen während der Mittagspause ein Hingucker. Immer wieder bleiben Mitarbeiterinnen und Mitarbeiter stehen und schauen sich das Fahrzeug von allen Seiten an. Auch die Felgen: Sie bestehen bei dieser Kleinserie zu einhundert Prozent aus recyceltem Aluminium. Eigentlich nur ein ganz kleiner Schritt in Richtung weniger CO2 bei der Autoproduktion.
Für BMW-Vorstandsmitglied Post dennoch wegweisend. Ziel des Unternehmens sei es "die Kreislaufwirtschaft innerhalb der Autoindustrie zu etablieren". Stahl, Aluminium, Glas und Kunststoff sollen künftig in hoher Qualität wiederverwertet werden. Das Unternehmen will den Anteil von Sekundärmaterial in einem BMW von derzeit 30 auf 50 Prozent auszubauen. "Die Rohstoffe unserer Fahrzeuge von morgen fahren schon heute auf der Straße", beschreibt Post das Konzept seines Unternehmens, ohne ein Datum zu nennen, wann das verwirklicht sein soll.
Wohl noch Jahrzehnte bis zur CO2-neutralen Produktion
Dass es bis zum CO2-frei produzierten Auto noch ein sehr weiter Weg ist, steht für Bednarz, den Experten für grüne Produktion in Ingolstadt, außer Frage. Während der CO2-neutrale Betrieb eines Autos "relativ einfach möglich ist", werde es bei der Herstellung vermutlich noch Jahrzehnte dauern.
"Es wird gigantische Anstrengungen brauchen, um die Produktionsprozesse von Stahl, Aluminium und Kunststoffen vollständig CO2-neutral zu bekommen." Das gilt übrigens nicht nur für die Autoindustrie. Auch die Produktion von Fahrzeugen für den öffentlichen Verkehr steht vor den gleichen Problemen.